Strategies to improve the safety of the construction business
Safety during the construction process is extremely important. After all, this is important for the customers because they want to reduce costs, and the contractor needs to focus on preserving the life and health of employees.
The industry regularly encourages builders to improve their safety performance. For businesses, project safety metrics are the piece that assembles the puzzle of your business viability. For these indicators not to let you down, it is important to use these 9 strategies.
Strategy 1: Conducting consultations on safety in the workplace
The Occupational Safety and Health Administration (OSHA) provides safety advice to identify possible risks. It's free and confidential.
You can seek advice not only on a new project but also check existing programs. In addition, a significant plus is that after such a consultation, you are exempt from OSHA checks for 1 year.
Strategy 2: Create a safety program
In addition to reducing the risk of injury and death, the safety program also reduces the cost of treating an employee after an injury or payment after a disability. It is impossible not to mention the indirect costs, the amount of which is reduced after the analysis of the Labor Safety Department. You do not bear the loss of money and time in matters of finding replacement workers, loss of productivity, rework and damage to the reputation of your company.
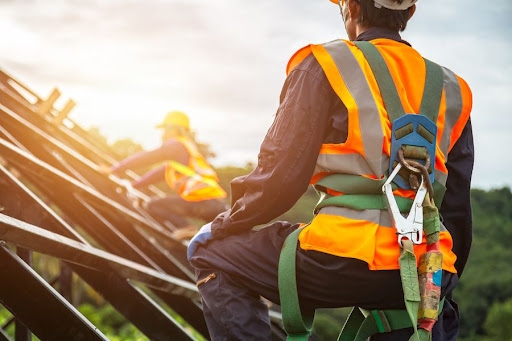
Strategy 3: Develop a safety program for all employee groups and occupations
Each demographic group periodically faces different risks. According to the US Bureau of Labor Statistics, from 1992 to 2017, the number of people aged 55 and older who work has doubled. But in 2017, the chance of these employees dying at work for job reasons more than doubled. This applies not only to the working staff but also to the project managers. Their figures are slightly lower - the chances of dying from industrial injuries in 25 years have become 1.5 times more. Nevertheless, this figure is quite significant.
In recent years, one in four builders was an immigrant. It also increases the risk of workplace injuries. All this is due to the language barrier. After all, to tell and show in detail, trying to explain, given the weak vocabulary - these are completely different things. To improve safety performance, it is important to review the acquired knowledge regularly.
Strategy 4: Consider the risks in your specialty to adjust your safety program
Morbidity rates represent statistically the number of injuries and illnesses per 100 full-time employees. The average accident rate for construction is 2.8. But it differs depending on the construction specialties. For example, framing contractors have a score of 4.5, and workers who perform finishing carpentry work have a score of 2.2.
Knowing the risk indicators helps the manager analyze and draw conclusions about how these risks can be reduced. If you set up the security program correctly, then the indicators with a high percentage of probability will drop significantly.
Strategy 5: Reduce rates of musculoskeletal disorders
Evaluate your methods of work to reduce the number of diseases in the musculoskeletal system. Although it is most often caused by excessive overexertion, it is possible to use ergonomic assessment tools to help you identify activities that endanger your employees promptly. In every industry, overvoltage accounts for a huge share of the cause and illness that leads to missed work. In addition to causing pain and suffering to the musculoskeletal system, they also exacerbate the general problem of dependence on painkillers.
Each enterprise can improve the situation of the national problem with the musculoskeletal system. The musculoskeletal system suffers due to repetitive movements, heavy loads that need to be lifted, and working in an uncomfortable position for a long time. Most often, the back is injured, the hands are in second place in terms of trauma, and the third and fourth places are shared by injuries of the shoulders and knees, respectively. Even though now the number of injuries has significantly decreased, they still confidently hold the lead among the most common non-fatal injuries.
Strategy 6: Pay close attention to temporary employees
Most often, temporary workers take part in the construction. Whether they come from a recruitment agency or some government program, chances are they won't be sufficiently familiar with safety and how to avoid the main hazards at a construction site. It is best to work with one recruitment agency where employees receive safety training appropriate to the job they are doing.
To check how much the employees know about safety precautions, you can conduct certain testing on them or appoint a responsible employee. If the hired worker does not speak the language, then safety training should be conducted in his native language.
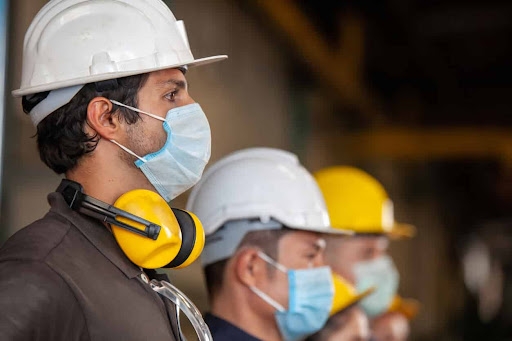
Strategy 7: Hiring new technicians
Since safety is an ever-important issue, it's worth empowering yourself with tools that help improve safety outcomes. Modern tools are called smart personal protective equipment. This technology helps to collect, analyze and produce results about the health of workers. This gadget can also issue an alert to workers who should change their behavior and their actions to avoid an accident.
Strategy 8: Make safety your first thought
Safety culture has become an important aspect of the company's activities. Many companies already use the most secure methods for work. It is important to analyze and understand the presence of hazards and think through actions to avoid risks. You must make this an important organizational aspect of your work to protect workers from injury and death.
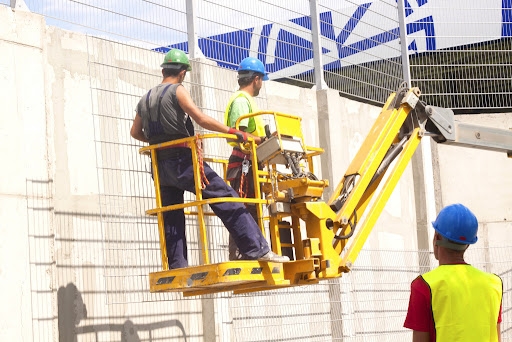
Strategy 9: Use leading indicators
You need to collect and analyze indicators to respond to ongoing security issues. By identifying leading indicators, you can take care of possible risks in advance and avoid them. By making indicators specific, measurable, and timely, you will receive the most complete instructions that will help prevent accidents at work.
Conclusion
Creating a safe working environment is not that difficult. It is only important to analyze all possible risks in advance to create comfortable working conditions for all your employees.